Introduction: The Dog Mansion - or - Knock-Down Dog House
I looked around for a commercial doghouse, but the ones I found didn't meet my design criteria - and they were kind of ugly - so, I decided to build my own.
Design Criteria:
- Had to be a KD (Knock-Down) design in case I wanted to transport or ship it.
- Had to be light enough for me to move it around the yard by myself
- I wanted it to be reconfigurable - i.e. change door/window locations - or remove walls all together.
- Insulated with some solar-warming capacity
- "Sittable" - since Mac likes to get up on top of things - kind of like Snoopy
- Sit up off the ground to protect it from water and make it easy to clean under it.
- Couldn't cost more than a good "commercial" dog house.
After sketching out a few ideas, I came up with a design that meets all the criteria I had laid out. Keep in mind that this house was designed for the size and weight of Mac - so it might be too big or too small for your dog. You want to have the interior large enough for your dog to stand up and turn around, as well as lay out full length - but not too much bigger than that since in colder weather the dog's body heat will be the main source of heat for the doghouse. The door opening should be *just* big enough for your dog to duck into - so - I measured Mac's shoulder width and height and worked with those rough dimensions.
I wanted the house movable so that I could reposition it in the backyard based on the season. In the Summer, I put it up against the house where it's in shade most of the time, and in Winter I move it out to four paver blocks I've embedded in the yard so that the house gets as much sun exposure as possible. The solar "heating" works pretty well - the inside of the house during the Winter stays about 15 - 25 degrees (F) warmer than the outside air during the day (Mac sleeps in a kennel indoors at night).
The basic structure is a knock-down frame with torsion-box walls. Torsion boxes - the same principle used in constructing most doors these days - are *very* strong and rigid for their weight, and they also allow for plenty of room for insulation.
Overall cost was about $375 - and you could cut $75 off of that if you left out the window. I put a window in for two reasons: 1) to allow for sunlight to pass through and warm the interior during the winter (I have a dark-colored mattress in there) and 2) to allow air-flow during warmer months. Another nice thing about this design is that the walls can be removed and switched around (or left off) if you decided, for example, you wanted to change which sides the door and window were on. The house can be "knocked-down" (disassembled) into a roof assembly, corner posts, wall panels and floor assembly fairly quickly if the need should arise. If you didn't want this feature, you could eliminate it and make construction even easier.
Materials:
- 2x4 framing lumber
- 1/2" plywood
- 1/8" Melamine sheet (sometimes called "tileboard")
- 4x4 posts
- Polyurethane construction adhesive
- Roof Edge Flashing
- Roofing Paper
- Rigid Insulating Foam
- Exterior Sheathing (embossed OSB in this case)
- Roof material (scrap rubber mat from local gym)
- Corner trim - plastic
- Roof "struts" - Baltic Birch scraps from another project
- Window Screen
- Furniture Bolts
- T-Nuts
- PVC Pipe
- Exterior primer and paint
- Silicone sealant
- Various screws, staples, etc
Step 1: Build the Main Frame
Dimension your lumber:
I prefer to re-dimension store-bought lumber - I don't like dealing with rounded edges and faces that aren't flat - but a person could probably work around these little details. The 4x4 posts (actual 3-1/2" x 3-1/2") were jointed and planed down to 3" x 3", and the 2x4 stock (actual 1-1/2" x 3-1/2") was sawn and planed down to 1-1/4" x 2" (the 2" dimension matches the thickness of the rigid foam).
Build the main frame:
The corner posts were cut to length and the tongues were cut on a table saw with a dado blade, however, careful use of a circular saw and chisels would work, too. Clean, flat, square edges are pretty important here.
The roof and floors are a basic ladder frame with the cross-members let into shallow dados on each side. The dados are probably overkill - but that's just the way I roll - lol. The floor frame was skinned on the bottom with 1/2" OSB sheathing (Oriented Strand Board or Chip Board) and on the top (the "floor" of the dog house) with 1/2" plywood. The top frame was skinned on the inside (ceiling) and the top with 1/8" Melamine sheet stock. ALL panels were attached with construction adhesive and mechanical fasteners - either screws or staples.
The roof and floor frames are designed to "capture" the "tongues" that are machined onto the ends of the corner posts. Basically, the posts have a tongue (double half-lap joint) that slips down into a square hole formed by the sides of the frame pieces and a filler block. The easiest way to ensure good alignment of the bolt holes through the frame and post tongue is to assemble the frame, clamp it together, and then drill the holes through your pieces. A furniture bolt is then slipped through a hole drilled in both the frame and the tongue of the post and threaded into a t-nut secured to the inside of the tongue (see illustration). It sounds more complicated than it is. There is a recess around the hole (made with a spade bit) for the bolt on both ends to keep the head of the furniture bolt and the flange of the t-nut from interfering with assembly.
Once the corner posts are in and everything is bolted together (incidentally, removing these 8 bolts would allow the frame to be disassembled), the bottom (OSB) is installed, followed by insulation, and then by the "floor" (plywood) of the structure. The "top" (melamine) is installed, the frame insulated, and then the "ceiling"(melamine) is installed. All of these use construction adhesive and pneumatic fasteners - mostly staples - to create very strong and torsionally rigid frames.
I decided to prime and paint the frame at this point since I would be using oil-based enamel and it would be the easiest time during construction to move around and get at all the parts. I was very concerned with moisture and sealing the wood - I wanted to be sure that water would have a very hard time sneaking into the frame and doing any damage.
Step 2: Build the Roof
The roof is constructed much like an airplane wing and is very strong. I needed a shape that would shed water, but not be too steep or uncomfortable for Mac to sit on - and it had to be strong enough to support my weight as well. The bottom of the roof panel is 1/8" melamine, the "ribs" are Baltic Birch plywood (scraps from another project) and the main "skin" is plywood. The skin needed to be bent to conform to the ribs, and the easiest way is via a technique called "kerf bending" where a series of partial longitudinal cuts ("kerfs") are made at increments on the table saw. The spacing is arbitrary and is based on the thickness of the material and the radius of the curve being bent - it takes a little experimenting but it's easy enough to figure out the spacing using scraps. These "kerfs" allow the panel to be easily bent over a structure. The kerfs close up as the plywood bends, and if they are filled with something like epoxy or construction adhesive you end up with a strong, curved panel. I suppose it could be argued that it wasn't necessary to kerf-bend the panel given how thick it is (only 1/2") and how shallow the arc, but I didn't want to have any static stresses working on the roof and I didn't want to wrestle with it while trying to put it together. I have stood on this roof with nary a creak or groan from the structure - it is very strong.
Before attaching the skin, I wanted to make sure that I wouldn't have heat building up inside the roof structure, so I cut holes to act as "eave vents" to facilitate airflow through the roof "chambers." I didn't want to provide home for wayward spiders or hornets so I surrounded each hole with a ring of adhesive and pressed in some pieces of window screen to help keep the critters out.
The roof skin was attached to the ribs with staples and construction adhesive. When the adhesive was dry, I used a belt sander to clean up the edges. I then primed and painted all of the exposed edges thoroughly - giving it all at least two coats of house paint for a good water seal.
The roof assembly was glued to the top of the main frame with polyurethane construction adhesive and then covered with roofing paper. The edges were trimmed out with metal drip-edging which was followed by the surplus gym mat cut to size and secured in place with a couple of stainless steel screws through washers. The mat is pretty heavy, so there's no need to glue it down or secure it at more than two points (on the center-line). This minimal attachment gives the mat the latitude it needs to grow and shrink with temperature changes without curling or bubbling up, and it keeps it from blowing off or sliding off when Mac jumps up or down off of it - it works very well.
Step 3: Building the Feet
To get the structure up off the ground, I needed something strong and non-absorbent - and something that would let me slide the house around on concrete without splintering or falling apart. Luckily, there is a store in my town that stocks all kinds of damaged shipping goods, unclaimed raw materials, and surplus crap of all descriptions. It's like a giant garage sale for men - lol. I found a piece of 3" nylon rod in one of the surplus piles which worked perfectly for this application, but I'm sure there are other solutions as well.
I cut 4 1/2" long "pillars" from the rod using a chop-saw, beveled their bottoms on the router table, and attached them to 4" aluminum plates (cut on the table saw with a metal-cutting blade) using screws threaded into drilled and tapped holes in the pillars. I primed and painted the pillars with rattle-can paint to protect them from UV light (sunlight breaks the plastic down over time) and make them look better, and then attached the assemblies to the bottom frame with screws.
Having the dog house up on "stilts" keeps water away from the structure, makes it harder for critters to crawl up into it, and makes it easier to clean under when blowing off the patio with a leaf-blower.
Step 4: Build the Walls
The walls are simple torsion boxes - very much like the floor and ceiling. They are a pine and foam core skinned in melamine on the inside and textured siding board (OSB) on the outside. The opening for Mac was based on his proportions - basically by measuring the height and width of his shoulders (he has to duck to get in and out). You don't want to make the door too big as it will let out too much heat that builds up when the dog is inside in cooler weather. I fit the wall frames to the frame openings pretty closely because *part* of the structural integrity - specifically "racking" resistance - of the house is enhanced by these panels. Breaking from traditional construction, I used miter joints at the corners... instead of butt joints..... for no particular reason. The outer sheathing panels were cut to the exact size of the sides of the main frame dimensions.
Once the frames were built, foam was cut and fitted to fill the voids in the "solid" parts of the wall. The inner skin was then bonded to the frames and that assembly was then bonded and screwed to the outer sheathing. I waited to cut the holes for the door and window until after the panels were glued up - it's much easier to use a pattern bit and a router to cut out the openings after the panels are together as opposed to cutting a hole and then hoping it aligns with your frame. At this point, the window was installed and sealed with silicone, and the door opening was trimmed out with plastic corner trim. I did a test assembly of the house to identify any problems (there weren't any) - so I removed the walls and primed and painted them as I did the roof. The walls are attached to the corner pillars and upper and lower frames with decking screws driven through the "flange" around the outer edge of the panels.
Step 5: Corner "Columns"
Since the edges of the wall panels were exposed at the corners I needed something to make them more safe and attractive. I settled on using pieces of 2" PVC pipe as "corner guards". I cut the pipe to length on my table saw, and then cut out a 90-degree section of the pipe. The pipes were primed and painted and then attached at the corners with two 3" long screws that screw into the corner of the corner posts. More than once I've been glad they're there - I think they've prevented some pretty good scrapes from happening.
Step 6: Conclusion
That's about it. I've been really pleased with this doghouse - and Mac has too. He definitely considers it *his* house. There have been a few winter days and nights that Mac had to spend outside, and it's kept him toasty warm during those times (I have a custom mattress in there now). In the summer, it offers a shaded and insulated shelter that has good airflow - it doesn't really get any hotter than the ambient temperature inside. The portable nature of it allows me to move it around the yard to whatever location is best for the season - which is a great advantage - and if I had to move it to another house, it could be broken down and moved pretty easily. After three years, the only upkeep has been a little bit of paint touch-up here and there - but other than that, it looks pretty much brand new. I hope this inspires you to build your own "dog mansion" - and while your at it - Guys, if you're married, build it really well since you may occasionally have to spend the night out there yourself - lol
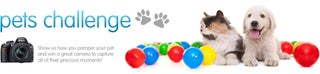
Grand Prize in the
Pets Challenge